Content
At Goerner Bionics, every innovation writes its own story.
As the world's largest consumer of plastics, innovations in the packaging industry already have sustainability status themselves. This is because they promote awareness of the problem where it is still lacking and stimulate truly healthy competition with all those who, like us, are fully committed to minimising environmental impact.

InnoWays is the innovation process as we understand it at Goerner Bionics. Every single product that can reduce the use of single-use-plastics is a gain for our environment.
We still remember how time-consuming an early development project with a partner was, how long it took when we discovered that the technology for these products was not yet technically mature and that we had to be involved in its development. Toolmaking also needs to be continuously developed to make new process technologies and applications possible. Giving up was a recurring theme. But we decided back then to carry on, and after step A we also proceeded to step B. Today, we are proud to show off products that are already looking forward to their market launch.
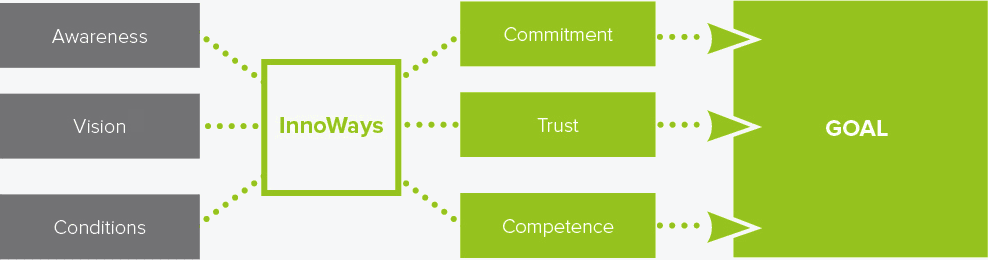
Packaging on behalf of the environment.
Goerner has only one goal: minimising the environmental impact. This joint mission makes us allies and partners.
Our guiding vision is to preserve an environment worth living in for as many living beings and habitats as possible.
In concrete terms, this means that we pool all our expertise and resources to work fully towards our vision.
As a result, our developments have only one direction. Sustainability by minimising the environmental impact. For all our products.
On this premise, we are already looking forward to the next development tasks with our current and future partners.
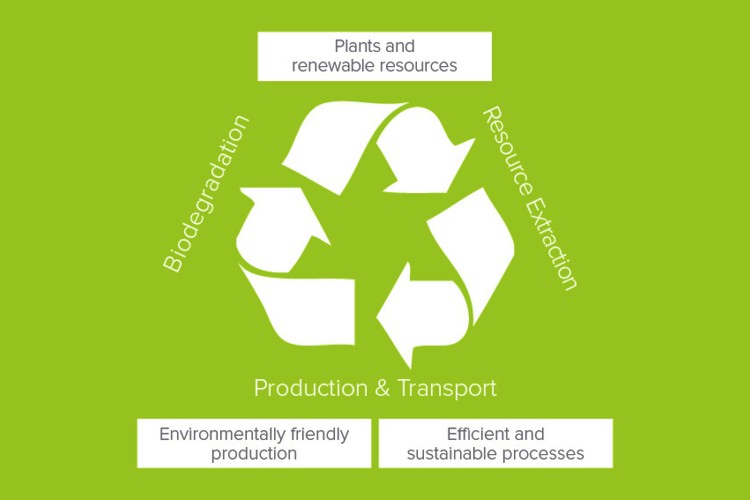
Innovation in Progress.
The human relationship between Goerner and its partners is extremely important. For us, clear communication and a fundamental understanding of vision, goals and mutual commitment are essential requirements for mutual success.
We would like to express our sincere thanks for the trust you have placed in us. This also applies to those partners that we cannot name here, as ongoing projects are protected by confidentiality agreements.
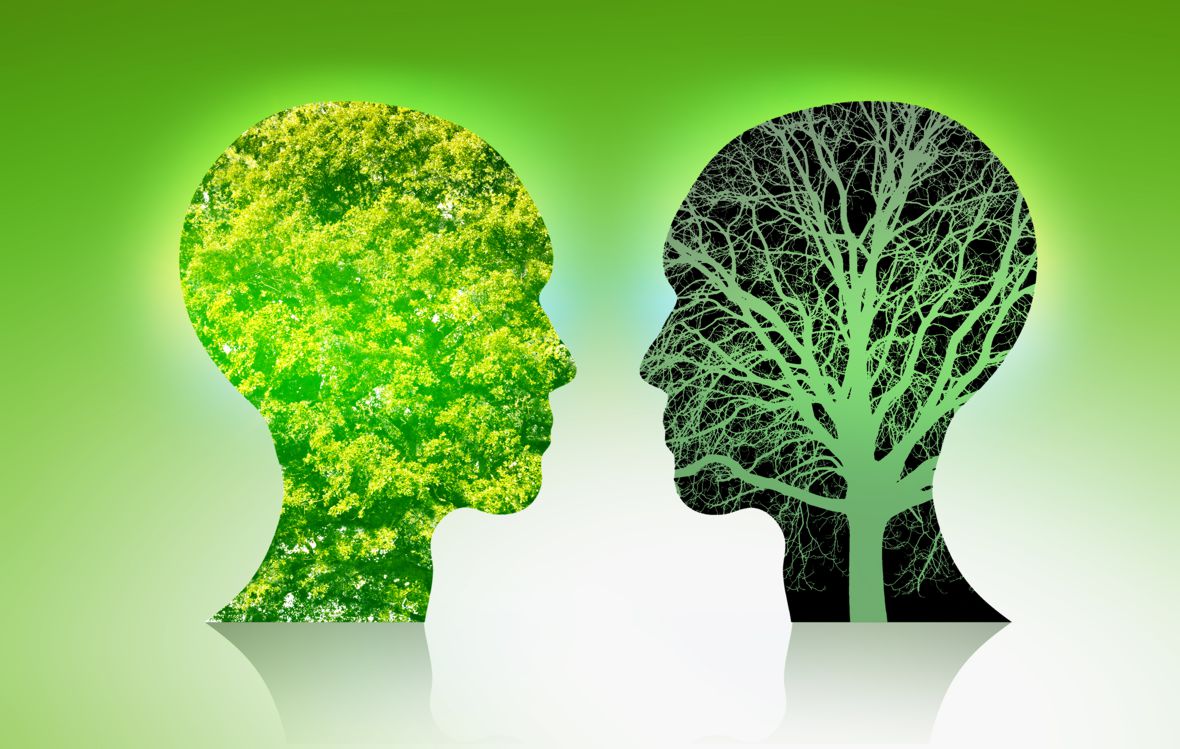
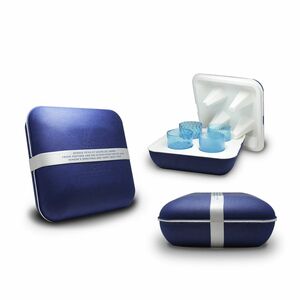
Nestlé gift box
Requirement:
Sustainable packaging solution consisting of renewable raw materials. The packaging should associatively emphasise the value of water and protect the high-quality contents for international shipping.
Material:
Pulp, 100% industrially compostable.
Manufacturing process used:
Normpack moulded fibre. The natural pulp fibre is suspended in water and moulded into three-dimensional packaging.
Special challenges:
Protecting the thin-walled Murano glass using a fixing on the base of the glass and leaving the glass edges free placed special requirements on our toolmaking department.
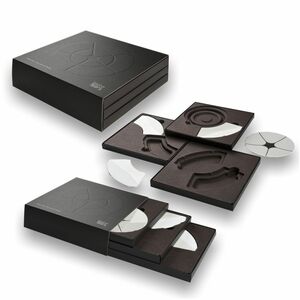
Nestlé gift packaging
The task:
High-quality gift and transport packaging for handmade designer plates made of renewable raw materials for international shipping. The tactile quality should reflect ecological significance and sustainability.
Manufacturing processes used:
Inlays: Normpack moulded fibre.
Outer packaging: Offset printing on pure pulp cardboard, die-cut and glued.
Implementation:
Single-colour printing of the rough cardboard inside and subsequent use as the outside. Pure pulp was used for the inner part which was dyed the same colour as the outer packaging. The assembly instructions were imprinted on the inlays.
Special challenge:
Colour matching between two different manufacturing processes.
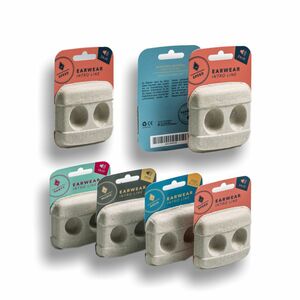
Neuroth earwear
Developed for Neuroth by Georg Wanker & Boschi.
Recycled cardboard played a major role in this sales and transport packaging. The sustainable and cost-efficient solution for NEUROTH products can either be shipped or given directly to the customer in the shop.
The packaging consists of cardboard, offset printed on both sides, onto which a moulded fibre part is glued.
In both manufacturing processes, recycled cardboard was deliberately used to draw attention to the sustainability and recyclability of the packaging product. This proved that pulp-based moulded fibre packaging is also very suitable for sensitive products.